News Categories
Contact Us
020-86988980
- Guangzhou Sinoth Import and Export Co., LTD
Tel: 020-8968-8980
Website:www.gzsynoth.com
Email: belinda@dginfa.com(24 hours online)
Phone: +86 189 2740 6786
Address: No 5, Jinshi Three Street, Shiling Town, Huadu District,Guangzhou City, Guangdong Province
News
Current Location:Home > News > Industry information
The Future of CNC Machining: Automation, Smart Manufacturing, and AI Revolution
Add Time:2025-06-23
The CNC machining industry is undergoing a profound transformation, driven by rapid advancements in automation, smart manufacturing technologies, and artificial intelligence. These innovations are reshaping production floors, redefining precision standards, and creating new paradigms in manufacturing efficiency. As we move deeper into 2025, several key trends are emerging that promise to elevate CNC machining to unprecedented levels of productivity and flexibility.
First. AI-Powered Optimization and Predictive Maintenance
Artificial intelligence has become the cornerstone of modern CNC machining operations, enabling machines to learn, adapt, and optimize processes in real-time:
AI-driven diagnostic tools: Companies like Mitsubishi Electric have developed NC MachiningAID, an AI-powered system that automatically analyzes machining data to detect tool wear, identify operational errors, and predict optimal tool change intervals without requiring specialized expertise . This reduces unplanned downtime by up to 30% in some implementations.
Process optimization: AI algorithms now analyze vast amounts of machining data to optimize cutting paths, reduce cycle times, and minimize material waste. Hexagon's ProPlanAI demonstrates how machine learning can slash CNC programming time by 75% while capturing institutional knowledge from experienced operators .
Self-learning systems: Frameworks like CNC-Net employ deep neural networks to simulate CNC operations and generate optimal machining parameters directly from 3D models, creating a low-cost alternative to manual programming . These systems continuously improve through operational feedback loops.
Second. Advanced Automation and Collaborative Robotics
Automation in CNC machining has evolved beyond simple repetitive tasks to sophisticated, flexible production systems:
Cobot integration: Companies like TM Robotics are deploying AI-powered collaborative robots that combine high-precision 3D vision with intuitive programming interfaces. These systems can manage multiple CNC machines, perform quality inspections, and adapt to new parts with minimal setup time-all without safety cages .
Lights-out manufacturing: With improved reliability and remote monitoring capabilities, many shops now run CNC operations unattended overnight. Automated pallet systems, robotic part handling, and in-process gauging enable continuous production with minimal human intervention .
Flexible manufacturing cells: Modern automation solutions emphasize modularity, allowing quick reconfiguration for different product batches. This is particularly valuable for industries like aerospace and medical devices that require frequent changeovers .
Third. Smart Manufacturing and Industrial IoT Integration
The fusion of CNC machining with IoT technologies is creating truly intelligent manufacturing ecosystems:
Digital twin technology: Manufacturers are implementing virtual replicas of CNC machining processes that simulate and optimize operations before physical production begins. This approach reduces trial-and-error and accelerates time-to-market .
Edge computing: By processing data directly at the machine tool, manufacturers achieve real-time analytics for immediate process adjustments. This is critical for maintaining tight tolerances in high-speed machining applications .
Cloud-based monitoring: Platforms like Hexagon's Nexus collect operational data from CNC machines across global facilities, enabling centralized performance analysis and best practice sharing . This supports data-driven decision making at enterprise scales.
Fourth. Sustainable and Energy-Efficient Machining
Environmental considerations are driving innovation in CNC equipment design and operation:
Energy-efficient designs: New CNC machine tools incorporate regenerative braking, low-energy cooling systems, and optimized drive technologies that reduce power consumption by 20-40%compared to previous generations .
Circular economy practices: Manufacturers are prioritizing machines designed for longevity and upgradability, along with systems that facilitate chip recycling and coolant recovery .
Renewable energy integration: Some forward-thinking facilities are powering CNC operations directly with solar and wind energy, supported by smart energy management systems that align heavy machining operations with renewable generation peaks .
Fifth. Advanced Machine Capabilities and Multi-Function Platforms
CNC machine tools themselves are becoming more sophisticated and versatile:
5-axis dominance: At recent trade shows like CIMT2025, over 60% of exhibited machining centers featured 5-axis capabilities as standard. These machines now achieve micron-level accuracy at high speeds .
Hybrid manufacturing: The line between subtractive and additive manufacturing is blurring, with CNC machines increasingly incorporating laser deposition
First. AI-Powered Optimization and Predictive Maintenance
Artificial intelligence has become the cornerstone of modern CNC machining operations, enabling machines to learn, adapt, and optimize processes in real-time:
AI-driven diagnostic tools: Companies like Mitsubishi Electric have developed NC MachiningAID, an AI-powered system that automatically analyzes machining data to detect tool wear, identify operational errors, and predict optimal tool change intervals without requiring specialized expertise . This reduces unplanned downtime by up to 30% in some implementations.
Process optimization: AI algorithms now analyze vast amounts of machining data to optimize cutting paths, reduce cycle times, and minimize material waste. Hexagon's ProPlanAI demonstrates how machine learning can slash CNC programming time by 75% while capturing institutional knowledge from experienced operators .
Self-learning systems: Frameworks like CNC-Net employ deep neural networks to simulate CNC operations and generate optimal machining parameters directly from 3D models, creating a low-cost alternative to manual programming . These systems continuously improve through operational feedback loops.
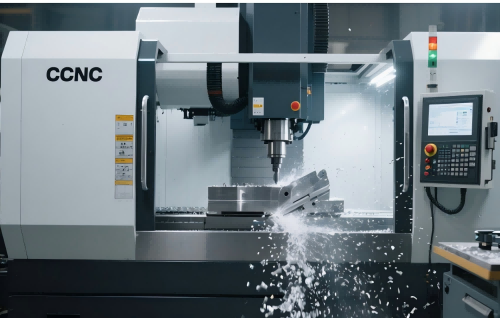
Automation in CNC machining has evolved beyond simple repetitive tasks to sophisticated, flexible production systems:
Cobot integration: Companies like TM Robotics are deploying AI-powered collaborative robots that combine high-precision 3D vision with intuitive programming interfaces. These systems can manage multiple CNC machines, perform quality inspections, and adapt to new parts with minimal setup time-all without safety cages .
Lights-out manufacturing: With improved reliability and remote monitoring capabilities, many shops now run CNC operations unattended overnight. Automated pallet systems, robotic part handling, and in-process gauging enable continuous production with minimal human intervention .
Flexible manufacturing cells: Modern automation solutions emphasize modularity, allowing quick reconfiguration for different product batches. This is particularly valuable for industries like aerospace and medical devices that require frequent changeovers .
Third. Smart Manufacturing and Industrial IoT Integration
The fusion of CNC machining with IoT technologies is creating truly intelligent manufacturing ecosystems:
Digital twin technology: Manufacturers are implementing virtual replicas of CNC machining processes that simulate and optimize operations before physical production begins. This approach reduces trial-and-error and accelerates time-to-market .
Edge computing: By processing data directly at the machine tool, manufacturers achieve real-time analytics for immediate process adjustments. This is critical for maintaining tight tolerances in high-speed machining applications .
Cloud-based monitoring: Platforms like Hexagon's Nexus collect operational data from CNC machines across global facilities, enabling centralized performance analysis and best practice sharing . This supports data-driven decision making at enterprise scales.
Fourth. Sustainable and Energy-Efficient Machining
Environmental considerations are driving innovation in CNC equipment design and operation:
Energy-efficient designs: New CNC machine tools incorporate regenerative braking, low-energy cooling systems, and optimized drive technologies that reduce power consumption by 20-40%compared to previous generations .
Circular economy practices: Manufacturers are prioritizing machines designed for longevity and upgradability, along with systems that facilitate chip recycling and coolant recovery .
Renewable energy integration: Some forward-thinking facilities are powering CNC operations directly with solar and wind energy, supported by smart energy management systems that align heavy machining operations with renewable generation peaks .
Fifth. Advanced Machine Capabilities and Multi-Function Platforms
CNC machine tools themselves are becoming more sophisticated and versatile:
5-axis dominance: At recent trade shows like CIMT2025, over 60% of exhibited machining centers featured 5-axis capabilities as standard. These machines now achieve micron-level accuracy at high speeds .
Hybrid manufacturing: The line between subtractive and additive manufacturing is blurring, with CNC machines increasingly incorporating laser deposition